Recycling capacities for lithium-ion batteries will exceed demand in Europe for the time being
The recycling of lithium-ion batteries (LIB) will play a key role for Europe in order to gain access to strategic raw materials. In addition to scale up existing pilot projects, announcements of new plants and the cancelling of recycling projects have been observed for around a year. This blog post provides an update on an article from August 2024 and discusses the latest developments.
Lithium-ion battery recycling has been the focus of intense attention for several years, particularly due to European legislation and the rise of e-mobility and battery production. It not only enables the environmentally friendly disposal of used batteries, but also provides access to strategically important raw materials for battery production in Germany and Europe.
Geopolitical uncertainties, such as interrupted supply chains and (threatened) high tariffs on global material chains and international value streams, highlight how important it is to establish and expand the recycling infrastructure in Europe in order to enable the circular use of important raw materials. Although various challenges to recycling projects have been discussed in the public press for around a year, a look at the current and expected battery recycling industry in Europe still gives hope that a European circular battery economy is in focus.
Current and announced recycling sites for lithium-ion batteries in Europe
The interactive map in Figure 1 shows the recycling facilities expected to be installed by mid-2025 and announced for the coming years with corresponding capacities for lithium-ion batteries in Europe, as well as their operators. The announcements in particular refer to the maximum site capacities that have been stated.
For better differentiation, sites that only deal with so-called pretreatment – i.e. deactivation, dismantling and the production of so-called black mass – are highlighted in blue (the so-called spokes). Even though fractions such as aluminium, copper and plastics are (or can be) recovered in this process, the majority of material recovery takes place in refinement (in so-called hubs), where valuable metals in the cathode, such as lithium, nickel, cobalt and manganese, or the anode material graphite, are usually recovered (or can be recovered) using pyrometallurgical or hydrometallurgical processes. For a more detailed differentiation between Spoke and Hub, see the article from August 2024.
Proximity to battery material supplier, battery cell manufacturers or car manufacturers is a recognisable driver for the location of recycling infrastructure. This can be seen, for example, in Germany's automotive areas, in Eastern Europe, on the Scandinavian shoreline and in northern France. Car manufacturers such as Mercedes-Benz in Kuppenheim operate their own recycling facilities close to their production networks. AESC recently officially opened its battery cell plant in northern France. Automotive Cells Company (ACC) already operates cell production lines here. At the same time, recycling processes from research-related pilot projects or smaller plants are being transferred to industrial scale, for example at Altilium Metals, Tozero and Cylib.
However, since mid-2024, projects have been repeatedly postponed or halted (e.g. Eramet, BASF, Umicore). The reason for this is that the ramp-up of battery production in Europe is slower than expected just a few years ago. Financing in particular is currently posing major challenges for companies: for example, the insolvency of Northvolt led to the closure of Revolt Ett's recycling hub in Sweden. The Canadian company Li-Cycle has also filed for insolvency, although its German spoke plant is to continue operating for the time being. These two companies alone have announced capacity expansions of up to 100 kilotonnes per year (kt/a) by 2030, which will now not happen.
Figure 1: Existing, announced and stopped recycling sites for lithium-ion batteries in Europe (as of July 2025)
Overall, battery recycling is very diverse and can be carried out using different combinations of processes – there is no single recycling route. In Europe, hydrometallurgy is clearly emerging as the core process for refining. Pyrolysis is only used in isolated cases in pre-treatment, or pyrometallurgy as a (partial) process in refining, e.g. at Umicore or Nickelhütte Aue. Pretreatment in the spokes does not always include black mass production, but sometimes only distinct process steps such as housing dismantling or testing for second-life applications.
Individual recycling projects cover the entire recycling stream at a single location, i.e. both pre-treatment (spoke activities) and refinement (hub activities). These are only classified as hubs, but we map it to both capacities, whereby the processing capacity corresponds to the maximum total mass of batteries treatment per year at the respective location. Usually, recyclers refer to processing capacity in terms of (kilo) tonnes per year of end-of-life batteries (EoL); see also the following section on Figure 2.
The pretreatment sites are scattered across Europe and thus fit well with the spoke concept. In contrast, sites for processing black mass are often located in areas with good infrastructure or close to battery material producers or automotive clusters. This is partly due to the fact that lithium-ion batteries are transported as hazardous goods, which makes transport expensive. The onward transport of black mass from the spokes to the hubs is technically and regulatory easier to implement.
Installed recycling capacity for lithium-ion batteries in Europe could rise to more than 400,000 tonnes per year by 2026.
Public information is available on the capacity of most recycling plants. However, as not all plants have the same recycling depth or process steps, it is not easy to determine the total European capacity from the sum of these figures.
Nevertheless, the capacities can be added separately for pretreatment and refinement. For better classification, the refinement capacities are further converted into a black mass equivalent (processing of black mass) if no black mass capacity data is available. All capacities do not reflect the actual capacities that can be called upon in practice or current utilisation, but rather the publicly reported (targeted) maximum processing capacity of a site. The projection also does not distinguish between different recycling strategies (focus on lithium, focus on nickel/manganese/cobalt, focus on graphite), but includes the mass of input streams per year that can (theoretically) be processed.
In Europe, the cumulative capacities of the hubs currently (Q2 2025) exceed the capacities of the spokes by approximately 290 kilotonnes per year, with approximately 270 kilotonnes per year. Both figures are cumulative processing capacities for EoLbatteries and production waste in tonnes, which companies usually state in their official communications on plant size, and are underneath the extrapolated total from the 2024 analysis. The current capacities of holistic recyclers (pretreatment and refinement activities at one location) comprise several tens of kilotonnes per year (e.g. Stena, BASF, Nickelhütte Aue, Snam). Looking at refinement in terms of the ability to process black mass, the total capacity in black mass equivalent is approximately 130 kilotonnes per year. One tonne of used batteries corresponds to approximately 400 kilograms of black mass. However, these figures should be interpreted with caution, as Europe is currently a net exporter of black mass and the actual capacities operated are therefore likely to be significantly lower, particularly in the refining sector, for economic reasons.
In Europe, the total capacity of spokes for LIB recycling is expected to rise to 420 kilotonnes per year by the end of 2026. This includes the capacities that have been announced but not yet officially started. Compared to 2024, total capacity is therefore expected to increase by roundabout 150 kilotonnes per year. By 2030, a total of around 520 kilotonnes per year of capacity for pretreatment has been announced. The expected battery recycling capacity in Europe is therefore increasing despite several cancelled projects (i.e. Eramet in France, BASF in Spain). The majority of companies in European battery recycling plan to establish several sites for their recycling activities in the medium to long term.
The announced capacities for the recovering of raw materials and material refinement in the hubs are also increasing significantly. By 2026, the pretreatment capacity will roughly relate to the refinement capacity. By 2030, the announced total capacity for refinement (820 kilotonnes per year handling capacity) will significantly exceed the return volume. In 2030, this would correspond to a processing capacity for black mass of around 350 kilotonnes per year.

The »demand side« of battery recycling is also difficult to quantify. There are no official statistics on the return rate of EoL batteries (especially EV batteries) and production scrap. In our approach, the quantity of used batteries and battery scrap to be treated is extrapolated from current data using a quantification model, taking into account factors such as battery production capacity, EV and battery life, and the development of vehicle export markets.
A comparison of the announced recycling capacities with the forecast LIB return volumes of EoL batteries and production scrap indicates that the cumulative capacities will exceed demand in the coming years. By 2030, the forecast return volume will rise from currently around 100 to up to 270 kilotonnes per year (Figure 2). This means that in the coming years, the supply of already installed and announced processing capacities will exceed demand in the form of EoL batteries and production scrap. In particular, the stagnating or delayed expansion of cell production in GWh factories, which leads to low quantities of new scrap, amends the expected return volume for battery recycling in 2030 by around 40 per cent (approx. 150 kilotonnes) downwards compared to the 2024 estimate. Nevertheless, pilot plants or new cell production sites will also offer emerging market entry opportunities for battery recyclers in the future to establish local material cycles through scrap recycling, e.g. via direct recycling in the factory.
German and European companies possess considerable technological expertise and market presence in European LIB recycling.
In recent years, European companies have managed to compete with foreign companies by establishing new sites or expanding their facilities. Currently, around 30 percent of spoke capacity in Europe is provided by Asian and American companies (Figure 3). In 2024, this share was still around 40 percent. The commissioning of new sites by European companies (including BASF, Librec and Mercedes-Benz) last year significantly increased Europe's share of total capacity. In terms of hub capacity, Asian and American companies account for around one third of total capacity. Although traditional metal recyclers and smelters use pyrometallurgical processing, most of the (announced) projects currently use combined mechanical and hydrometallurgical processes for material recovery.
Overall, the analysis shows that European players are already very active in the European LIB recycling market. Future expansion plans and announcements for new sites show that Europe is not only technologically capable of LIB recycling, but that a "domestic" recycling industry is also being promoted actively. However, uncertainties remain as to which site with which capacity can be maintained in the coming years to meet the sharp increase in return volumes from e-mobility from 2030 onwards.
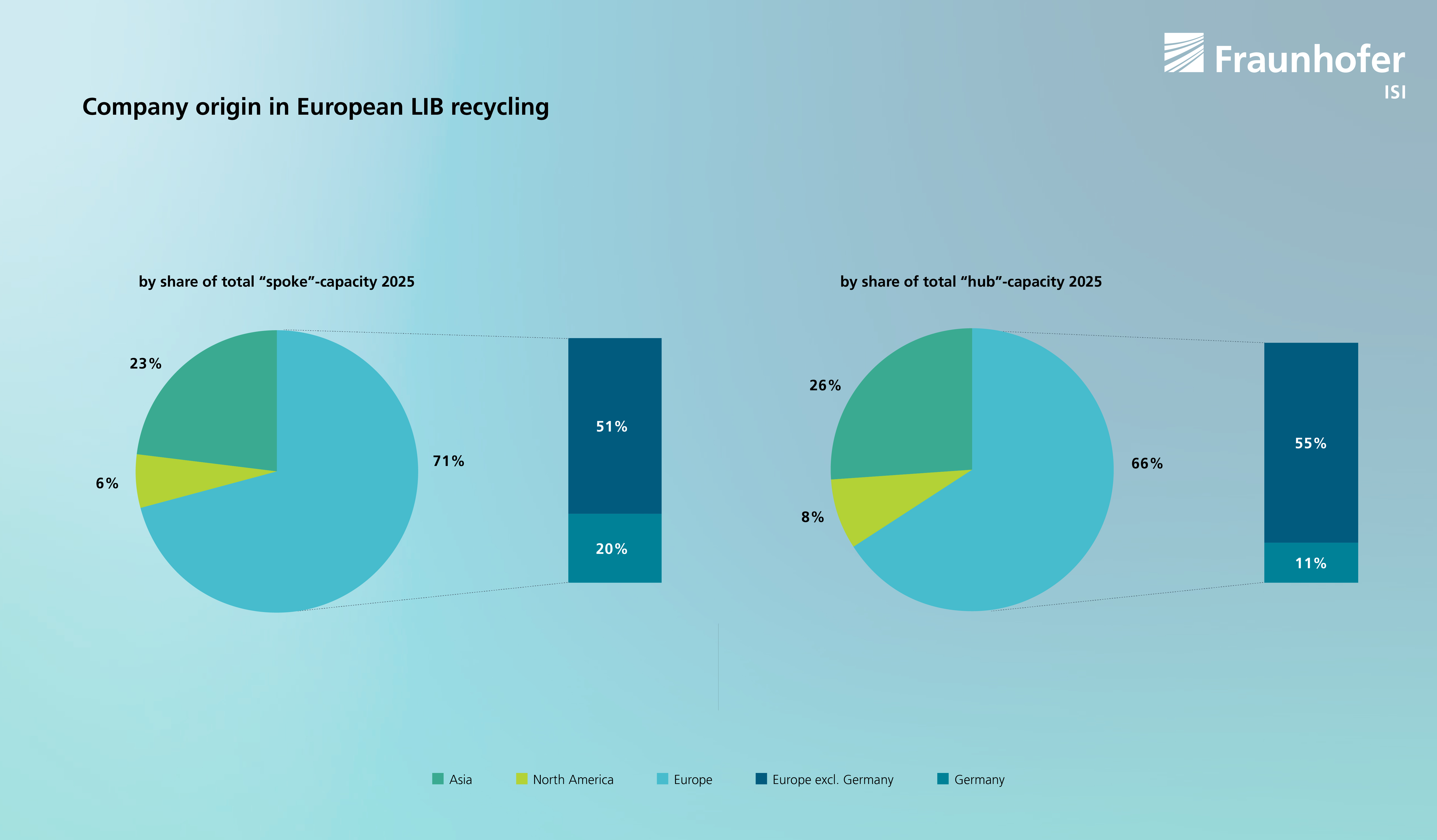
In summary, it can be observed that the establishing and expansion of recycling plants for LIB recycling is currently developing very dynamically. The smaller scalable and more local pre-treatment sites have advantages over refinement plants, as the latter are even more dependent on large input quantities for economical operation (economies of scale, very high investment required). European refining is facing strong global competition, e.g. from very large processing capacities in Asia, especially in China. While China is now actively seeking to import black mass, European legislation has taken initial measures this year with a new waste classification for black mass to make exports from Europe more difficult. In accordance with the anticipated return volume in Europe and the current regulatory framework, operational recycling capacity is likely to continue to converge with input streams.
The data used comes from the research projects BEMA On (funding 03XP0621A) and BETSY (funding 03XP0540B) funded by the Federal Ministry of Research, Technology and Space.
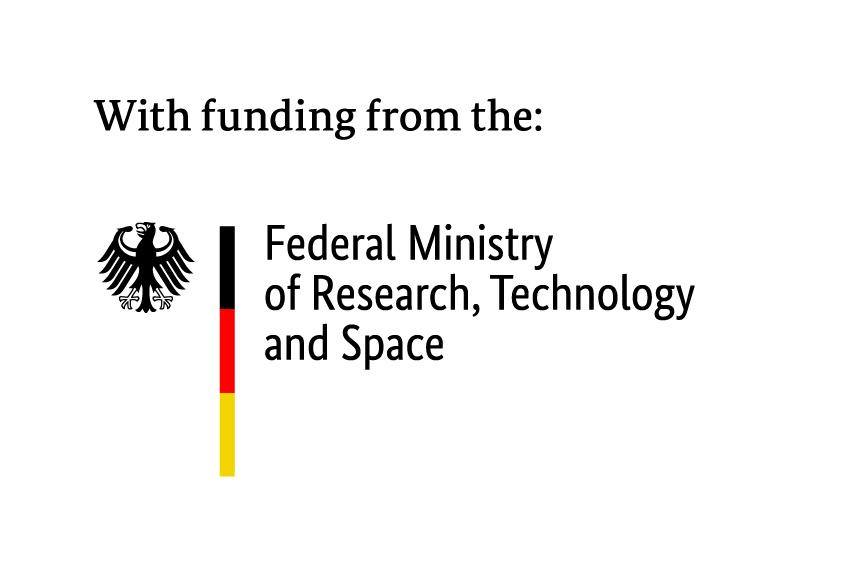
If you notice any missing or incorrect information about a location on our map, please contact us at maximilian.stephan@isi.fraunhofer.de.