Europe expands recycling of lithium-ion batteries: Focus on capacity development, demand analysis and market players
The need for recycling capacity for lithium-ion batteries is growing. How Europe will meet it - and which companies are investing at which locations.
Resource availability and environmental impact play a key role in lithium-ion battery (LIB) production. To minimize environmental impacts (such as carbon footprint) and reduce dependency on imported raw materials, recycling of LIB plays a central role for Europe. The recycling technologies used have steadily evolved in recent years, and in perspective allow overall recovery rates of more than 90 percent (excluding O2).
With the rapidly growing sales of electric cars, electrically powered trucks, stationary storage as well as batteries in numerous other applications, a strongly increasing demand for the recycling of LIB can be expected in the foreseeable future. While so far the majority of LIB recycling capacity is located in East Asia, especially in China, capacity for LIB recycling is currently also being built in Europe.
Current and announced recycling sites for lithium-ion batteries in Europe.
The map in Figure 1 shows the lithium-ion battery recycling facilities installed by the end of 2023 and those announced for the coming years in Europe and their operators. The particularly high number of recycling sites in Central Europe is striking. This is often due to proximity to battery material producers, battery cell manufacturers or automotive manufacturers. In the coming years, however, countries such as Spain and the UK will also increase their capacities and thus diversify the project situation in Europe.
Numerous plants are planned from the outset so that they can increase their capacity if necessary. An example of this are companies such as Northvolt, SungEel HighTech and EcoBat, which are planning to expand the recycling capacity of their sites by more than 150,000 tons per year by 2030.
The recycling sites can be divided into "spokes" and "hubs" according to recycling depth - i.e. depending on what the input and output materials of the recycling process are (designations adapted from Li-Cycle). Spokes are capable of performing the first steps of battery recycling. In this process, spent batteries are discharged, disassembled and mechanically processed into the so-called black mass. This includes the cathode and anode active materials, which contain most of the valuable metals.
Hubs can also perform the second stage of battery recycling. Here, the black mass is refined using (electro)chemical hydrometallurgical processes or a polymetallurgical approach, allowing valuable materials such as cobalt, nickel and lithium to be recovered. In Europe, just under half of the sites are hubs with the capability to recover battery raw materials (marked with red dot in Figure 1).
Spokes are located decentrally for optimal logistics, while hubs can be established centrally for black mass processing. This is partly due to the fact that the transport of lithium-ion batteries to Spokes is classified as a dangerous goods transport. As a result, the arrangements for transport are more complex and cost-intensive than for black mass.
Recycling capacities for lithium-ion batteries in Europe will increase to 400,000 t/a by 2025
Information is available on most recycling facilities regarding their recycling capacity. However, since not all facilities have the same recycling depth, these capacities cannot simply be added up. Summing the capacities of the spokes allows an estimation of the capacity of the first recycling steps up to the black mass. Thus, it is possible to estimate approximately the amount of battery that can theoretically be recycled. However, since individual recycling plants carry out both processing to black mass and further processing at the same site, the potential recycling quantity is underestimated.
In the EU, capacity for the first steps of LIB recycling will increase to 160,000 tons per year by the end of 2023, spread across 37 sites. Compared to 2020, capacities have increased by more than 100,000 t/a with the commissioning of 13 major recycling facilities. Another 16 plants are planned and will bring further capacity gains.
With the announced new plants and expansions alone, capacities are expected to reach 400,000 t/a in 2025. A comparison of the planned recycling capacities with the projected return volumes of recycled batteries and production rejects indicates that the planned capacities will exceed demand in the coming years (Figure 2).
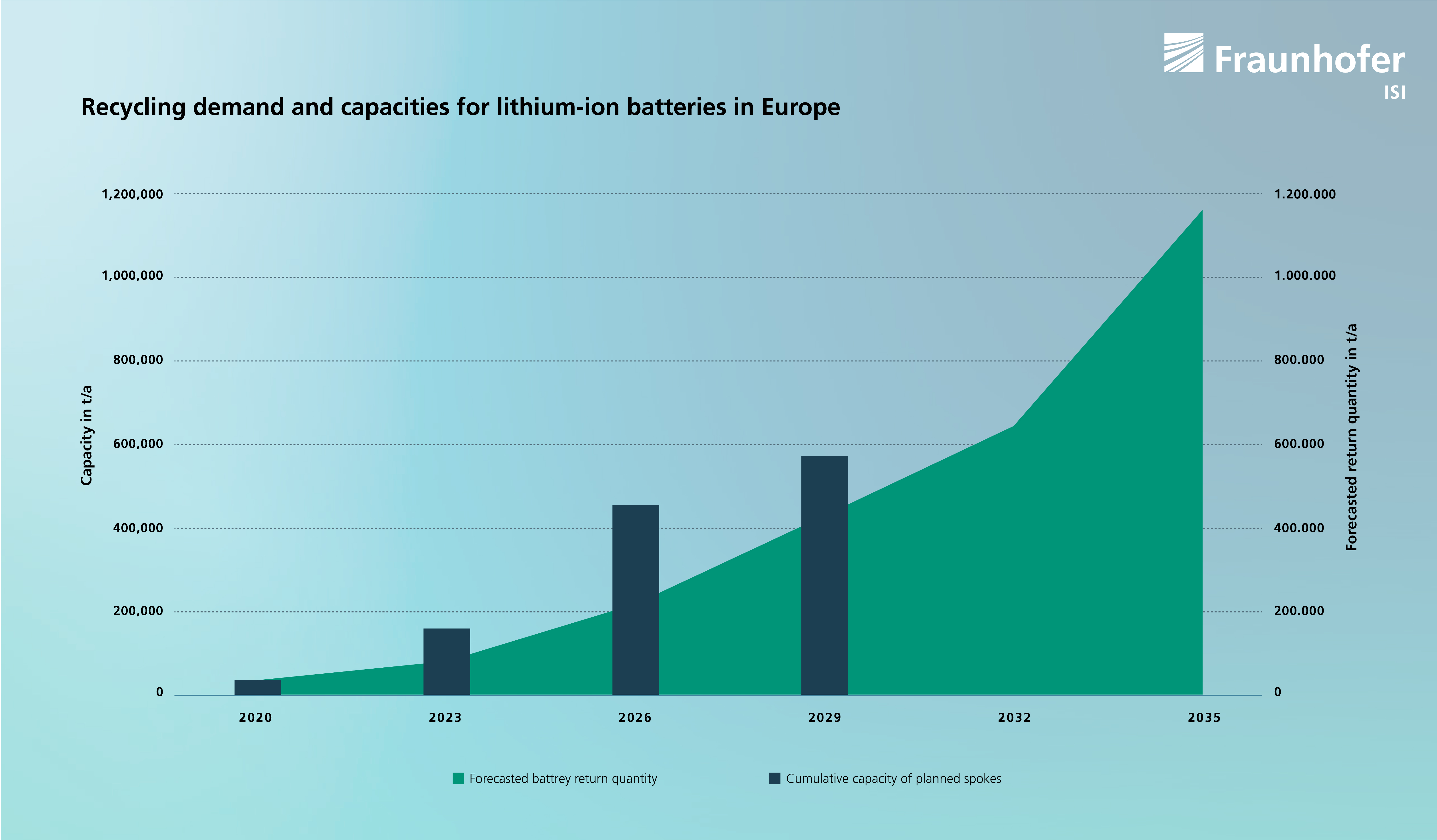
The high market dynamics in the European region are driven, among other things, by the establishment of battery cell production sites: This is because, particularly during the ramp-up phase, but also during ongoing operations, relevant quantities of production scrap are generated that have to be recycled. For example, the high density of recycling facilities in the eastern German region can be explained by the battery cell production facilities of Tesla, Microvast and Farasis. In addition, SungEel HighTech is installing its new recycling plant to recycle production rejects not far from LG Chem's cell manufacturing facility in Wroclaw, Poland.
European companies hold their own against Asian and American competition in battery recycling in the EU
Analyzing the origins of the plant operators, the large number of European companies stands out. In recent years, they have been able to hold their own against foreign competition with new sites and plant expansions. Currently, around 30 percent of the capacity in Europe is processed by Asian and American recyclers. SungEel from South Korea and the American Ecobat operate the largest plants.
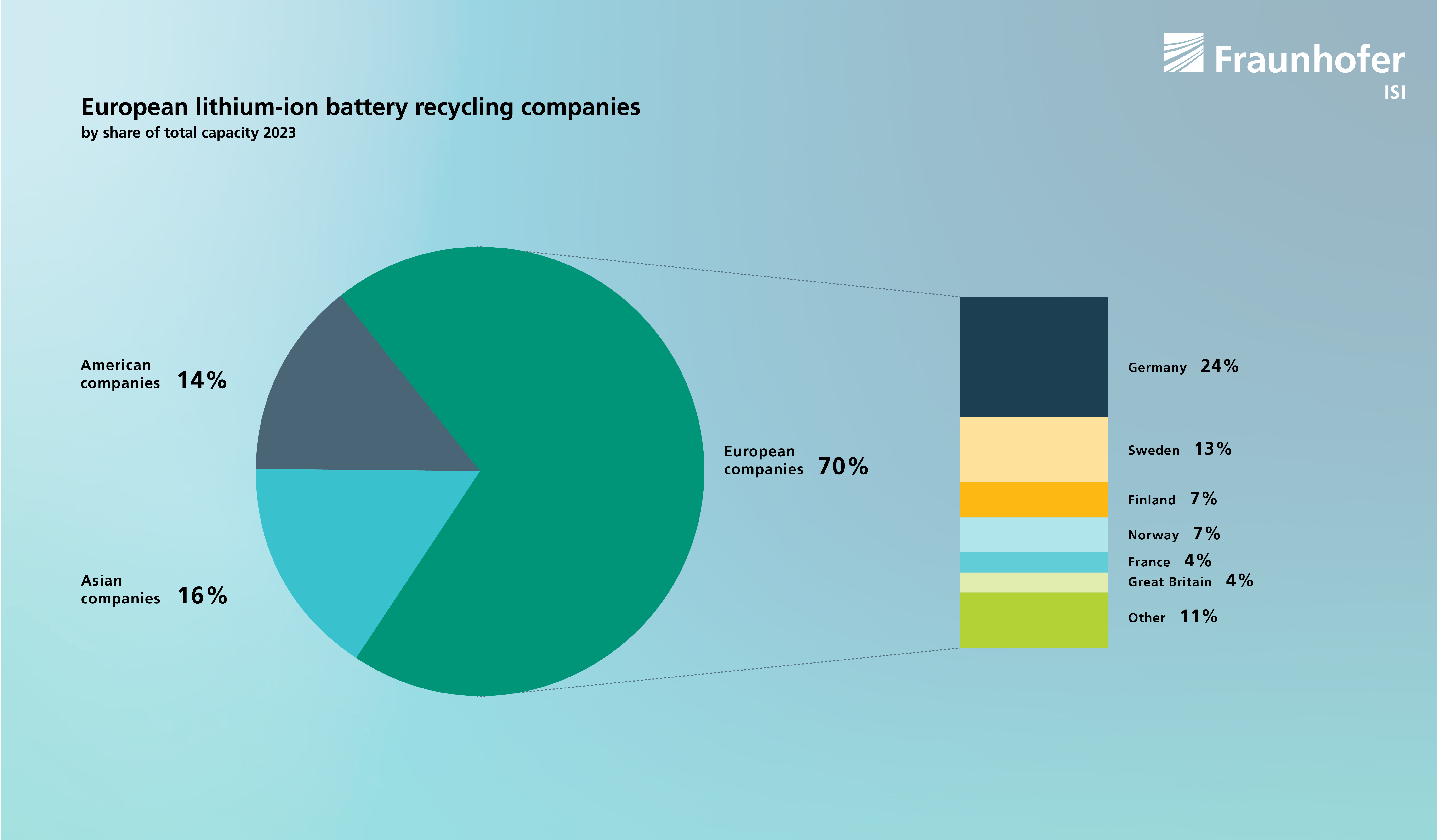
European companies such as Northvolt, Altilium Metals and Librec have greatly increased their capacity announcements. Northvolt plans to increase its capacity in Sweden by 100,000 t/a by 2030, while Librec aims to increase capacity to 200,000 t/a by 2026 with plants in Poland, Spain, Italy and Germany.
Overall, however, the current size ratios are expected to remain, as Asian companies are also looking to increase capacity in the coming years through expansions (SungEel in Germany, Poland, and Hungary) and new builds (EcoNiLi entering in Spain).
The LIB recycling plants identified are operated by many different companies. Among them are larger corporations such as Erlos (a spin-off of WP Holding) and BASF, as well as joint ventures such as Primobius GmbH (between Neometals Ltd. and SMS Group GmbH). Some companies are already active in the battery industry or are established recyclers of lithium-ion batteries (e.g., Stena Recycling, Accurec, Redux and TES). In addition, OEMs such as Mercedes-Benz and Volkswagen have also established initial sites in Kuppenheim and Salzgitter. Furthermore, Renault with Veolia, Honda with Snam, Audi with Umicore and Volvo with Stena Recycling are also participating in LIB recycling through joint ventures and partnerships, although most of these are still pilot projects. In addition, leading cell manufacturers and material producers such as Northvolt and Umicore have entered the competition for battery recycling in Europe.
There are also start-ups in the corporate landscape. However, these are currently responsible for a negligible share of recycling capacity. Nevertheless, several companies such as Cylib or Tozero Recycling have been founded in recent years and have brought new processes and procedures to the market. For example, the lack of a network to other players in the value chain (e.g., collection, logistics, battery production) proves to be a barrier to market entry. Established players have an advantage here, e.g., through existing contracts with cell manufacturers for the acceptance of production rejects or established processes in logistics.
The data used in this article comes from the BEMA2020 research project, which is funded by the German Federal Ministry of Education and Research (grant number 03XP0272B).
![BMBF_CMYK_Gef_M [Konvertiert]](/en/blog/themen/batterie-update/recycling-lithium-ionen-batterien-europa-kapazitaeten-bedarf-akteure-markt-analyse/jcr:content/fixedContent/pressArticleParsys/textwithasset_208279_160495028/imageComponent/image.img.jpg/1669109419622/BMBF-gefoerdert-2017-en.jpg)
Last modified: