Analysis of global battery production: production locations and quantities of cells with LFP and NMC/NCA cathode material
The cathode is a central component of a lithium-ion battery cell and significantly influences its cost, energy density, i.e. relative storage capacity, and safety. Two materials currently dominate the choice of cathode active materials for lithium-ion batteries: lithium iron phosphate (LFP), which is relatively inexpensive, and nickel-manganese-cobalt (NMC) or nickel-cobalt-alumina (NCA), which are convincing on the market due to their higher energy density, i.e. their ability to store electrical energy. Our analysis shows where in the world how much of which cathode material will be used in battery production and by when.
Global production of battery cells will increase sharply in the coming years, and cathode materials will be newly and further developed. Nevertheless, the market shares of these two technologies are expected to remain high until the end of the decade.
This can be attributed to several aspects. First, LFP and NMC/NCA cathodes are complementary technologies. They have different advantages and disadvantages that make these technologies more or less attractive depending on end-use requirements. Furthermore, both LFP and NMC batteries offer development opportunities. For example, the energy density of an LFP cathode can be increased with the help of manganese (LMFP cathode). For an NMC cathode, reducing the cobalt content while increasing the nickel content results in a cost reduction and energy density increase.
Advantages and disadvantages of the individual active materials
In terms of safety, LFP technologies offer advantages over more flammable NMC and NCA materials. They are also more resistant to high temperatures. However, LFP batteries have a lower energy density and therefore require more space to provide the same amount of energy.
NMC and NCA batteries can have higher costs due to limitations in the availability of raw materials. Cobalt mining is complex and therefore expensive. The price of nickel has also risen sharply at times in recent years. This is due, for example, to supply bottlenecks caused by the war in Ukraine and the associated speculation about supply shortages.
In electric vehicles, where achievable speed and the ability to drive longer distances are prioritized over price (upper class segment), NMC and NCA technologies seem to be more popular due to their higher performance. If price is the top priority, LFP-based batteries are used, for example, for larger vehicles such as buses or heavy-duty transport or for small vehicles. In stationary storage, the compactness of the battery does not play a central role, since there are no strict space restrictions as in electric vehicles. This points to a clear advantage of LFP batteries.
Analysis of worldwide production sites
The production of the individual cathode materials is market-driven. Whereas in Europe and the USA the high-performance and more expensive luxury vehicles are particularly well represented in the market, in China there are also many small cars with LFP cell chemistry. In the USA, the influence of Tesla and the NCA cathode material, used more or less exclusively by this manufacturer, is also clearly visible.
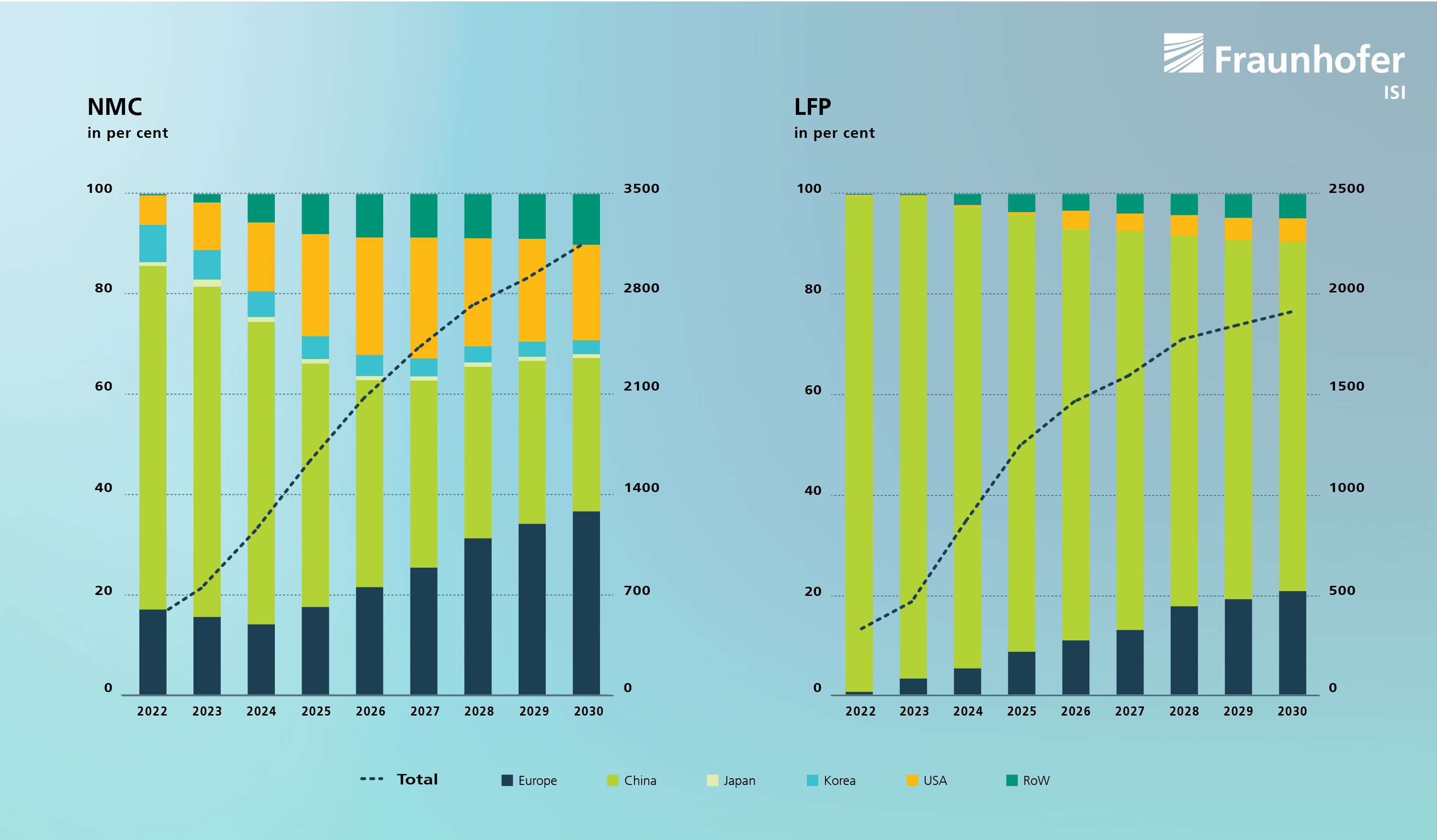
Worldwide production of batteries with LFP cathodes takes place mainly in China, where it accounts for just over a third of total battery production. In contrast, the production of battery cells with NMC cathodes accounts for slightly more than a quarter in China. By 2030, Chinese production will account for about a quarter of total global NMC cathode production.
In the USA, NMC and NCA cell production dominates. This represents about half of the total production in China. The U.S. share of global production of cells with NMC cathodes will only reach around 20 percent by 2030. LFP cell production in the U.S. turns out to be relatively small and thus also accounts for only a small share of global production.
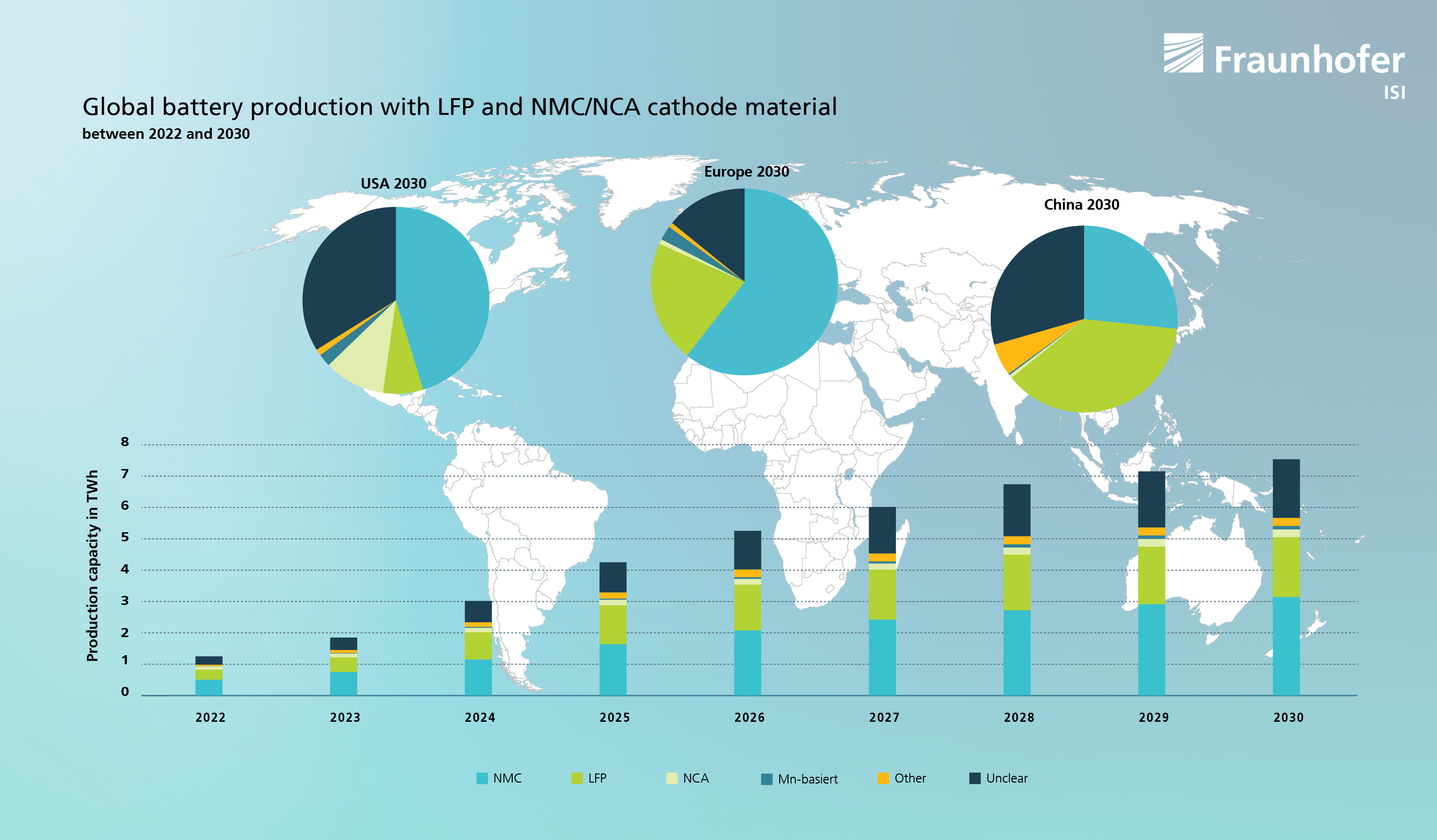
In Europe, the production of NMC battery cells will clearly predominate in 2030. In the course of the coming decade, European NMC battery cell production will therefore also account for an increasingly relevant share. In parallel, LFP cell production in Europe will also slowly increase and gain relevance.
Europe could produce more NMC cathodes than China in 2030
Chinese manufacturers such as China Aviation Lithium Battery (CALB) and Contemporary Amperex Technology Co. (CATL) account for a large share of LFP cathode production. In the production of NMC cathodes, manufacturers such as CATL, but also the Korean companies Sk On and LGES are active. In the case of NCA cathodes, the production of Samsung SDI and Panasonic is particularly relevant.
Currently, China dominates both NMC and LFP battery cell production. At least for NMC battery cell production, the U.S. and Europe will gain a significant share of global production by the end of the decade. If the announcements in Europe are actually implemented at the targeted rate, NMC battery cell production in Europe would even be larger than in China by 2030.
The data used in this article comes from the BEMA2020 research project, which is funded by the German Federal Ministry of Education and Research (grant number 03XP0272B).
![BMBF_CMYK_Gef_M [Konvertiert]](/en/blog/themen/batterie-update/globale-batterieproduktion-analyse-standorte-mengen-zellen-lfp-nmc-nca-kathoden/jcr:content/fixedContent/pressArticleParsys/textwithasset_208279/imageComponent/image.img.jpg/1669109419622/BMBF-gefoerdert-2017-en.jpg)
Last modified: