Solid-state batteries: Potential and challenges on the way to the mass market
Solid-state batteries are regarded as a promising further development of lithium-ion batteries. Different materials are available for the various components. Which ones could be successfully commercialized in (hybrid) cell concepts in the future?
Batteries play a decisive role in the electrification of transport, the intermediate storage of green electricity and thus the reduction of CO2 emissions. The current leading battery technology of lithium-ion batteries (LIB) with liquid electrolyte (Figure 1a) is being continuously developed, but is increasingly reaching its physical limits. Solid-state batteries (SSB, Figure 1b) promise higher energy densities and improved safety compared to liquid electrolyte LIB and could therefore represent the next major development step.
In an all-solid-state battery (ASSB), not only is the liquid electrolyte replaced with a solid electrolyte, but this newly introduced material also replaces the original (polymer membrane) separator. However, these cell types still face a number of challenges in production and realization. For this reason, cell manufacturers are increasingly developing hybrid solid/liquid LIB. In addition to a solid electrolyte, which usually serves as a separator, additional gel or liquid electrolyte is also used.
This blog post is based on a study published by Fraunhofer ISI ("Solid-State Battery Roadmap 2035+") and a publication by Justus Liebig University Giessen and Fraunhofer ISI ("A Roadmap for Solid-State Batteries"). Further details on the topic can be found in these publications.
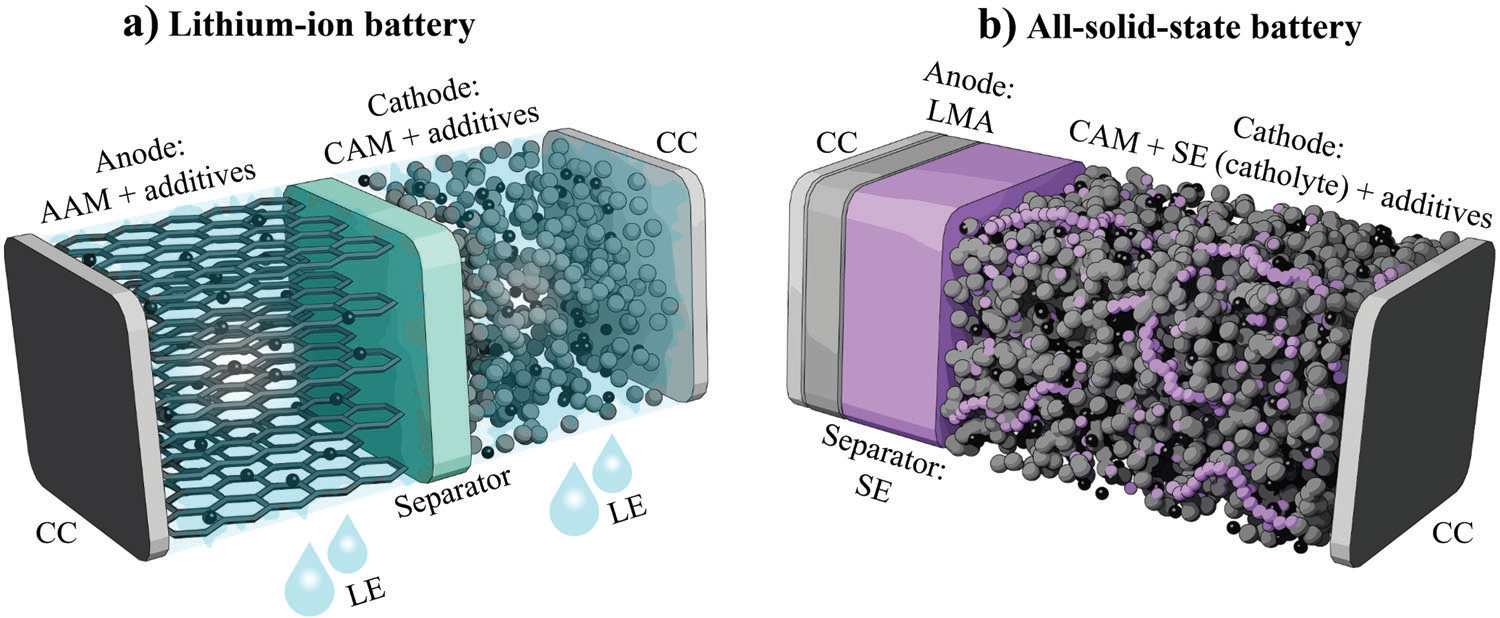
Components of solid-state batteries
As mentioned above, the structure of SSB differs from that of liquid electrolyte LIB due to the use of a new separator material or the (partial) omission of a liquid electrolyte. There may also be differences in the active materials (anode/cathode).
Anode active materials
Lithium metal anodes and silicon-based anodes are seen as promising alternatives to the currently most commonly used graphite anode in order to realize batteries with higher specific energies. Challenges in their use are production-related aspects, (electro)chemical stability with neighboring components and the volume change of lithium metal and silicon anodes during cycling and thus long-term stability. SSB cell concepts often rely on the use of lithium metal anodes in order to achieve high energy densities. Safe use of lithium metal anodes requires the use of a solid electrolyte.
Cathode active materials
The same cathode materials can be used in solid-state batteries as in conventional liquid electrolyte LIB. These include high-energy materials such as nickel-rich layered oxides (e.g. NMC, NCA), spinel oxides (e.g. LMO, LMNO) and more cost-effective materials such as olivine-type lithium iron phosphate (LFP). Due to their high capacities, layered oxides with a high nickel content are seen as particularly promising and could dominate the future of SSB cell development.
Solid electrolytes
Three classes of solid electrolyte materials are currently considered to be the most promising for use in solid-state batteries: Polymer electrolytes, sulfide electrolytes and oxide electrolytes.
Polymer electrolytes are inexpensive and easy to process, but have low ionic conductivities at room temperature and only low stability against high-potential cathode active materials. Sulfide electrolytes offer similarly high ionic conductivities as liquid electrolytes, but generally show limited (electro)chemical stability towards cathode and anode active materials. Oxide electrolytes show high (electro)chemical stability towards cathode and anode active materials, but are complex to process and have only low ionic conductivities, which limits their possible applications.
Promising cell concepts and their potential market entry
Polymer SSB, consisting of lithium metal anodes, a polymer electrolyte as a separator and as a catholyte (liquid electrolyte replacement on the cathode side) and an LFP cathode material, are already in use (e.g. in electric buses). However, this cell concept must be operated at elevated temperatures in order to ensure sufficient ionic conductivity of the polymer electrolyte. A further development of this cell concept, for example with NMC-based cathode materials, is under development and is expected between 2025 and 2030.
Sulfide SSB cell concepts generally use NMC-based cathode materials, sulfide electrolytes as separator and catholyte (and anolyte - i.e. the corresponding liquid electrolyte replacement on the anode side), as well as a lithium metal anode or a silicon-based anode. Both cell concepts (with a lithium or silicon anode) are considered promising and are expected on the market between 2025 and 2030.
Oxide SSB cell concepts generally also use NMC-based cathode materials, lithium metal anodes, an oxide electrolyte as a separator and a gel electrolyte as a catholyte. This cell concept is also expected on the market between 2025 and 2030. In the medium term, sulfide electrolytes could also be used as catholytes instead of gel electrolytes, thus replacing all liquid (or gel-like) components. Oxide SSB will therefore initially come onto the market as hybrid (liquid/solid) cell concepts. Overall, the trend is towards hybridization of cell concepts that use a combination of different solid electrolytes or a combination of solid and liquid electrolytes in order to exploit the best properties of the individual electrolytes.
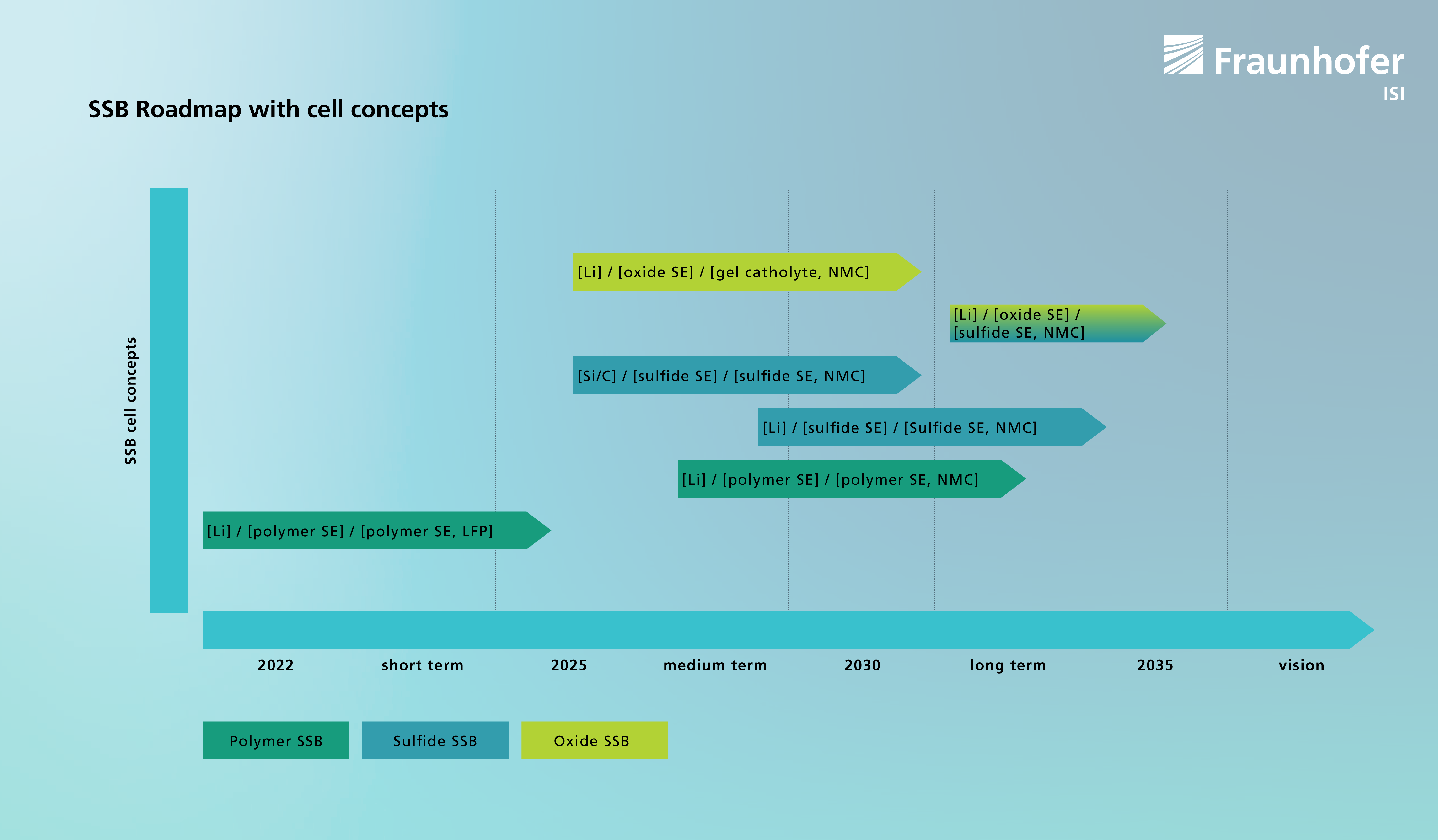
Applications of solid-state batteries
The development of solid-state batteries is mainly driven by electromobility and its quest for higher energy densities and therefore greater driving ranges. Polymer SSB are already on the market and are currently used primarily in electric buses. Sulfide SSB could initially find their way into the consumer sector and then probably be installed in electric cars before 2030. Oxide SSB are also promising for use in electric vehicles. In the long term, all types of solid-state batteries could also be used in stationary applications, provided that the costs per charging cycle are competitive.
Outlook
With the prospect of higher energy densities, improved safety and lower costs, solid-state batteries can be seen as the next evolutionary step of lithium-ion batteries. There are still some technical challenges, particularly with regard to the selection of materials, the compatibility of the various components and the production technologies for mass production. Strong R&D activities, fueled by great interest from the automotive sector in particular, suggest that these challenges can be solved. Ultimately, however, solid-state batteries will have to prove their competitiveness compared to liquid electrolyte LIB on the market, particularly in terms of cost, energy and power density.
The data used in this article comes from the BEMA2020 research project, which is funded by the German Federal Ministry of Education and Research (grant number 03XP0272B).
![BMBF_CMYK_Gef_M [Konvertiert]](/en/blog/themen/batterie-update/feststoffbatterien-markt-potenziale-herausforderungen-materialien-komponenten-zellkonzepte/jcr:content/fixedContent/pressArticleParsys/textwithasset_208279_1944787488/imageComponent/image.img.jpg/1669109419622/BMBF-gefoerdert-2017-en.jpg)
Last modified: